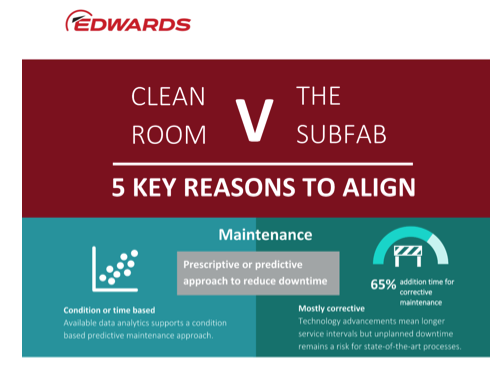
By Alan Ifould
At a time of renewed focus on digital transformation, business leaders are seeing just how important operational resilience is when meeting performance objectives. Fast and flexible operations from the clean room to the subfab are propelling customers ambitious growth targets, but how are customers navigating this landscape of change and where remains the unlocked potential?
This blog post and the next will work together. Here we will look at where we are now in our approach to service and support practices. Then in the next post we will look to the future: what is next for the direction of the market. To give structure to this discussion, we will look at these topics in the context of a service maturity model which provides an evaluation of the characteristics at each level. This model describes a progression from reactive maintenance through preventive maintenance to predictive and prescriptive maintenance. What are the advantages and disadvantages of each approach, and what are the challenges we face as we move from level to level? We will see that one characteristic of the progression is a trend toward automation and analytics, but in the end, human factors also play an essential role. A full list of characteristics is explored in more detail in Edwards Service Maturity Model.
New technologies like the internet-of-things, artificial intelligence, machine learning, big data, advanced analytics, cloud computing, and many more, are enabling the next revolution, often labelled industry 4.0. And already, the next phase, 5.0, which will leverage collaboration between increasingly powerful automation technologies and the unique creative potential of human beings, is on the horizon.
The evolving maturity of servicing and maintenance
As machines of all types have played a constantly growing role in all types of manufacturing, methods and approaches to supporting and maintaining those machines have also evolved. The service maturity model that we incorporate in our own model of Operational Excellence, describes a progression through five levels. The lowest level is to do nothing – worry about it later. The next is reactive maintenance – run to failure and fix it when it breaks. This is a risk-based strategy that looks at maintenance costs as a non-productive expense and focuses mostly on minimizing that cost. The next level up is planned/preventive maintenance. At this level manufacturers are beginning to look at the value added by maintenance through improvements in efficiency and performance. Maintenance is scheduled periodically to occur before the equipment is likely to fail. Essential components of this approach are determining the optimal period, standardizing performance and procedures, and finding opportunities for improvement. Predictive maintenance, the next level, is condition-based and relies on increased monitoring of operational parameters to predict imminent failures. It seeks to maximize the time between interventions while avoiding failures. The highest level in the progression is prescriptive, in which close collaboration between the user and the service provider and a shared commitment to continuous improvement promote a prescriptive approach to maintenance, or adjustments to machine operation that optimizes outcomes to achieve the user’s goals.
The progression described in the service maturity model allows us to look at where we are and where our customers are – so we can align and collaborate to achieve the desired outcome. It is important to realize that there isn’t a way to assign customers to a level on the scale. Different customers, different locations of the same customer, and even different products and participants within our own organization are often at different levels. Some of our on-chamber vacuum solutions are already approaching a proactive model while many of our sub-fab solutions are still managed with a run-to-fail approach. The service maturity model is most useful as a framework for determining the best next step in the continuous effort to improve user outcomes.
Challenges
The greatest challenges posed by the maturity progression are related to the increasing complexity at each level. Each higher level requires greater understanding of the user’s environment and process. At each level, the solutions must be more customized to reflect differences in processes. Each level requires more information to flow to characterize the state of the equipment and provide the basis for continuous improvement. The barriers are not always technical. For instance, they may be driven by organizational concerns about confidentiality and data security. Each level requires a broader view of the operational context and an increased understanding of other equipment and environmental variables that may affect performance and efficiency.
Some of these needs can be addressed by technical innovation in the design of the equipment, such as adding sensors to monitor relevant performance parameters or cloud storage of data to offer faster access to a larger data set. Others are cultural, such as overcoming historic biases against data sharing and suspicions about cloud storage security. Some technical innovations are still in the early stages of their own evolution. Machine learning, in which machines analyze their own performance and self-correct, are only beginning to take hold. Artificial intelligence may someday rival human intelligence in its ability to solve complex problems and implement goal-oriented solutions, but it is not there yet. These and other advanced technologies are still at a point where their recommendations require human review: we still (and likely will for decades to come) rely on the creativity of humans for innovative solutions. Still, they can offer significant value by reducing the amount review and alerting operators to suspect conditions. In any case they are tireless monitors that never need to eat or sleep.
Trust
One trend that runs consistently from bottom to top, through all levels of the service maturity model, is the need for increasing trust between user and provider. Our field service engineers comment frequently on its importance, whether it is confidence in their ability to repair a down system that has been run to failure, or willingness to accept a prediction that maintenance is required on a system that is apparently running well. Trust can result only from close collaboration over time that demonstrates not only competence but also commitment to continuous improvement and an intimate understanding of the user’s process and goals. This requirement for trust will keep humans in the process. You can learn to trust a machine, but ultimately, it is trust between humans, trust in their innovative creativity, that will lead us to the next level. In our next post we will look more closely at the essential role trust plays within this landscape of change.
To assess where your organization is on the services maturity scale, download the Services Maturity Infographic. Alternatively, further learning on operational excellence can be found on the Innovation Hub, edwardsinnovation.com/operational–excellence
Acknowledgements – I want to thank Matt McDonald, Dirk Gordon and Andrew Longley for their valuable insights and contributions to this discussion.